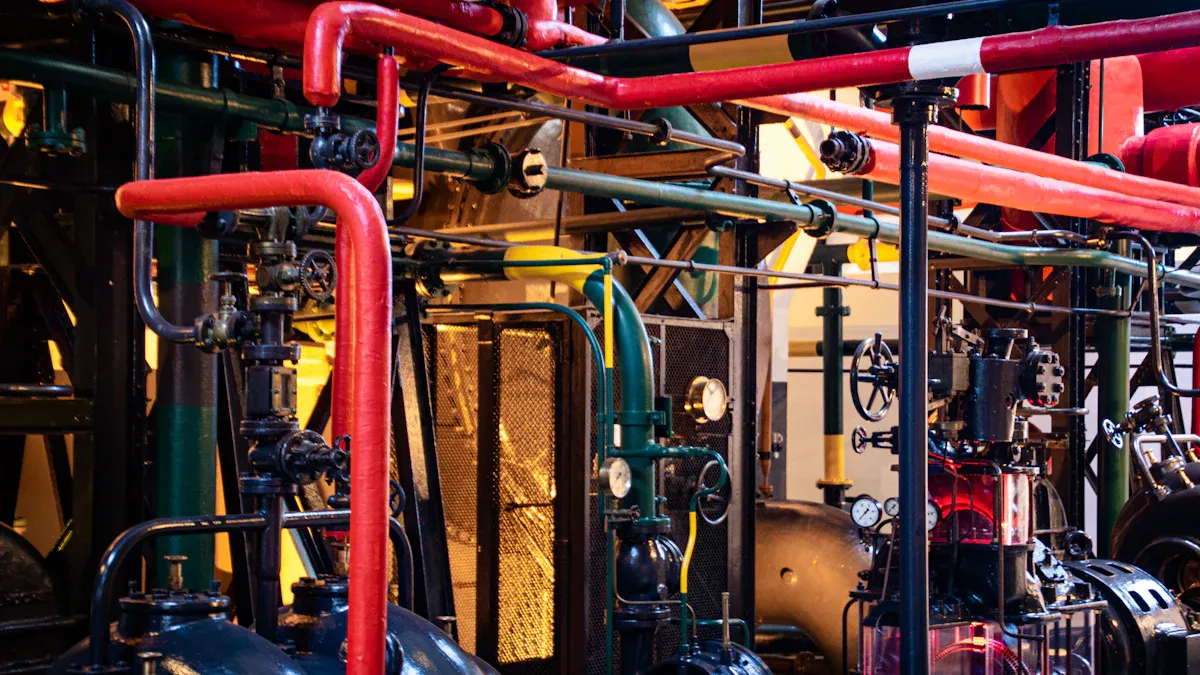
Image Source: pexels
In 2025, The best vacuum pump models undergo rigorous performance testing, ensuring high efficiency and long operational life. Matching the right pump type to each application remains critical. Selection depends on performance, energy efficiency, maintenance, and cost.
.jpg)
Key Takeaways
Choose vacuum pumps based on your specific needs like vacuum level, energy use, and maintenance to get the best performance and cost savings.
Rotary vane pumps offer reliable, low-cost solutions for general use but need regular oil maintenance and may risk contamination.
Liquid ring pumps handle wet or dirty gases well and work best in harsh environments, though they use more energy and need seal liquid care.
Dry screw pumps provide oil-free operation ideal for clean industries like semiconductors and pharmaceuticals, with lower maintenance but higher upfront cost.
Selection Criteria
Performance
Industrial buyers evaluate performance by examining how well a pump meets operational demands. They assign numeric importance weights to customer requirements, then map these needs to technical parameters using a relationship matrix. Each candidate receives a rating from 0 (worst) to 5 (best) for every requirement. This approach enables a clear, competitive analysis. Regular testing remains essential. Technicians measure vacuum levels and energy consumption to detect early signs of degradation. For example, a rotary vane pump with higher rated motor power can outperform a screw pump with lower power, especially at typical operating vacuum levels. Comparative studies show that rotary vane pumps evacuate faster and consume less energy than screw pumps under identical conditions.
Energy Efficiency
Energy efficiency plays a critical role in pump selection. Studies reveal that energy consumption in industrial systems can be reduced by up to 99%, depending on the application. Liquid ring pumps typically operate at 25% to 50% efficiency, with the largest models reaching nearly 60%. In dry roots pumps, motor loss accounts for almost half of total energy use, followed by friction and gas compression work. These statistics highlight the importance of evaluating actual operating conditions and pump design, not just nominal motor ratings.
Maintenance
Regular maintenance ensures reliability and extends pump life.
Maintenance frequency depends on pump type, usage, and environment.
Annual inspections are standard, but continuous or harsh operations require more frequent checks.
Key tasks include weekly oil checks, filter inspections, and monitoring noise or vibration.
Preventive maintenance involves annual specialist inspections of rotors, seals, and valves.
Performance tests verify vacuum levels, stability, and absence of leaks.
Maintenance records provide objective benchmarks for service intervals.
Cost
Total cost of ownership (TCO) includes purchase price, maintenance, energy use, downtime, training, and environmental compliance. Leading manufacturers offer resources and tools to help buyers calculate TCO for specific solutions. Market trends favor energy-efficient, oil-free, and dry pumps, which reduce contamination and disposal costs. Automation and smart monitoring further lower lifecycle costs by enabling predictive maintenance and real-time diagnostics. Examples include dry screw technology and variable speed drive pumps, which demonstrate significant savings through improved efficiency and reduced maintenance.
Vacuum Pump Types
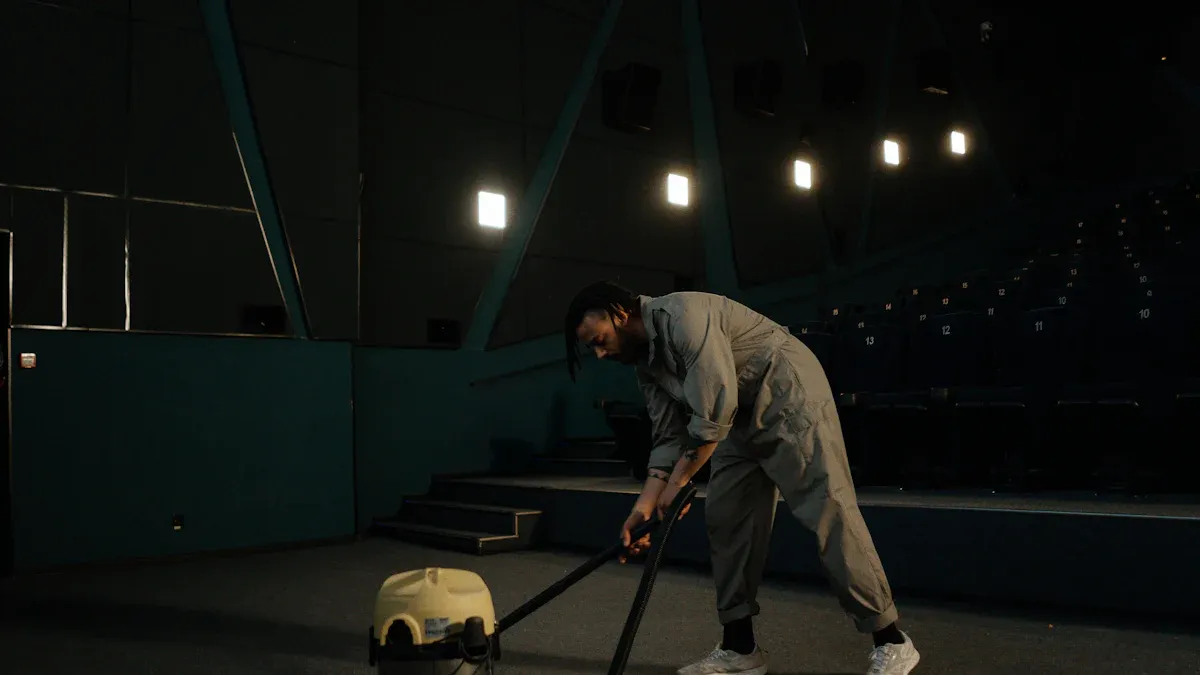
Image Source: pexels
Rotary Vane
Rotary vane pumps remain a popular choice for many industrial applications. These pumps deliver steady, pulse-free flow and handle moderate pressures effectively. Oil-lubricated rotary vane pumps achieve ultimate pressures as low as 10^-3 mbar, making them suitable for both industrial and laboratory use. Their oil system provides sealing and cooling, which enhances reliability and durability. Maintenance cycles usually involve oil changes every 500 to 2000 hours, supporting long service life.
Rotary vane pumps use high-quality, wear-resistant materials and precision-machined parts. This design slows mechanical aging and ensures consistent performance.
Rotary vane pumps require more routine maintenance than gear pumps but offer reliable long-term operation. Oil-lubricated models provide higher vacuum levels but may pose contamination risks. Dry-running versions reduce contamination and maintenance costs, though they operate at lower efficiency.
Liquid Ring
Liquid ring vacuum pumps excel in handling wet or contaminated gases. Their simple design uses a rotating impeller and a liquid seal, often water, to create vacuum. These pumps tolerate liquid and solid carryover, making them ideal for chemical, pharmaceutical, and power generation industries.
Numerical studies show several advantages:
Study / Author(s) | Type of Numerical Study | Key Findings / Advantages |
---|---|---|
Zhang et al. (2020) | Experimental and numerical study using xanthan gum sealing liquid | Energy savings of 21.4% by reducing wall friction and turbulence losses compared to pure water |
Rodionov et al. (2021) | Design and analysis of adjustable discharging port | 25% reduction in energy consumption and 10% increase in working speed due to improved efficiency |
Rodionov et al. (2019) | Mathematical and finite element modeling of rotating sleeve blades | Up to 40% reduction in power consumption due to reduced friction and space optimization |
.jpg)
Liquid ring pumps offer robust performance in harsh environments. However, efficiency decreases with increased rotational speed, and maintenance may involve managing seal liquid quality. These pumps remain a reliable choice for processes involving vapor or particulate-laden gases.
Dry Screw
Dry screw vacuum pumps represent a growing trend in contamination-sensitive industries. These pumps operate oil-free, making them suitable for applications in semiconductors, pharmaceuticals, and food processing. Their simple, compact structure contains no friction between pumping components, which reduces wear and extends service life.
Dry screw pumps provide a wide pumping speed range and large volume flow rate.
Oil-free operation eliminates contamination risk and lowers maintenance costs.
High initial acquisition cost can be a barrier, but long-term savings often offset this.
The deployment of 36 Busch dry screw pumps in cryogenic systems for superconducting radio frequency testing demonstrates their reliability. The system achieved a stable 74-hour cooldown period, supporting advanced research needs.
The market continues to shift toward oil-free and dry vacuum pump technologies. These solutions help industries meet strict contamination standards and reduce environmental impact.
Vacuum Pump Comparison
.jpg)
Image Source: pexels
Specifications
Industrial buyers compare vacuum pumps by examining several key specifications. These include ultimate vacuum, pumping speed, power consumption, noise level, weight, and lifespan. While many pumps may advertise similar ultimate vacuum levels, their real-world performance can differ greatly. For example, two pumps with the same ultimate pressure may have different pumping speeds at working pressure, which affects efficiency and wear. Performance curves that show pumping speed versus pressure help buyers understand how a pump will perform in actual use.
The following table summarizes typical specifications for leading industrial vacuum pump models:
Parameter | Rotary Vane Pump (Oil-Sealed) | Liquid Ring Pump | Dry Screw Pump |
---|---|---|---|
Pumping Speed | 100–400 l/min | 150–500 l/min | 120–450 l/min |
Ultimate Vacuum | ≤1 x 10⁻³ Torr | 33–80 mbar | ≤1 x 10⁻² Torr |
Power Consumption | 0.4–0.75 kW | 0.6–1.2 kW | 0.5–1.0 kW |
Noise Level | 50–60 dB(A) | 60–75 dB(A) | 55–65 dB(A) |
Weight | 23–35 kg | 40–70 kg | 30–50 kg |
Maintenance Interval | 500–2,000 hours (oil change) | 1,000–3,000 hours | 3,000–8,000 hours |
Typical Lifespan | 5,000–8,000 hours | 6,000–10,000 hours | 8,000+ hours |
Applications | Packaging, Lab, General Use | Chemical, Power, Pharma | Semiconductor, Food, Pharma |
Note: Ultimate vacuum and pumping speed alone do not fully describe a pump’s performance. Buyers should review performance curves and consider energy consumption at their specific operating pressures.
Application Scenarios
Vacuum pumps serve a wide range of industrial and laboratory applications. The choice of pump type depends on the process requirements, contamination sensitivity, and desired vacuum level. The table below outlines common scenarios and recommended pump types:
Application Category | Typical Scenario | Recommended Pump Type(s) | Brand Examples |
---|---|---|---|
Laboratory | Filtration, degassing, freeze drying | Oil-sealed rotary vane, dry rotary vane, hook & claw | Becker, Pfeiffer |
Material Handling | CNC, packaging, robotics | Oil-sealed rotary vane, dry rotary vane, hook & claw | Busch, Gardner Denver |
Packaging | Vacuum sealing, tray forming | Oil-sealed rotary vane, dry rotary vane | Atlas Copco, Busch |
Manufacturing | Chemical processing, electronics, food drying | Oil-sealed rotary vane, dry rotary vane, dry screw | Leybold, Pfeiffer |
Controlled Processes | Degassing, drying, distillation | Oil-sealed rotary vane | Becker, Busch |
Contamination-Sensitive | Semiconductor, pharma, food processing | Dry screw, dry rotary vane | Atlas Copco, Leybold |
Vacuum pumps play a critical role in industries such as semiconductors, pharmaceuticals, oil and gas, and food processing. For example, semiconductor manufacturing requires dry screw pumps to maintain contamination-free environments. Pharmaceutical production uses rotary vane pumps for vacuum distillation and drying. Food packaging relies on vacuum pumps for sealing and freeze-drying to preserve product quality.
Pros and Cons
Each vacuum pump type offers unique advantages and disadvantages. Buyers should weigh these factors based on their specific needs.
Rotary Vane Pumps
✅ Reliable for deep vacuum and general use
✅ Lower upfront cost
❌ Requires regular oil changes and maintenance
❌ Risk of oil contamination in sensitive processes
Liquid Ring Pumps
✅ Handles wet or contaminated gases well
✅ Robust in harsh environments
❌ Lower efficiency at high speeds
❌ Requires management of seal liquid quality
Dry Screw Pumps
✅ Oil-free operation eliminates contamination risk
✅ Lower maintenance and repair costs due to simple design
✅ Variable frequency drives can reduce energy use significantly
❌ Higher initial investment (about 20% more than oil-sealed pumps)
❌ May require specialized installation
Centralized vacuum systems with variable frequency drives offer higher energy efficiency and lower maintenance costs compared to multiple point-of-use pumps. However, they involve higher upfront investment and installation complexity.
Repairing a vacuum pump can be cost-effective for minor issues, but recurring failures may increase long-term costs. Replacing older pumps with new models improves reliability, energy efficiency, and often comes with a warranty, though it requires a higher initial outlay.
Choosing the Right Pump
Application Fit
Selecting the right vacuum pump starts with matching its features to the specific needs of the industry. Engineers and process managers consider several factors before making a decision:
Required vacuum level (rough, high, or ultrahigh)
Flow rate and pumping speed
Chemical compatibility with process gases
Lubrication needs and contamination risk
Maintenance frequency and ease of service
Cost and operational efficiency
Different pump types suit different applications. Rotary vane pumps deliver high performance and flow but need regular oil maintenance. Diaphragm pumps offer chemical resistance and dry operation, making them ideal for sensitive or corrosive processes. Liquid ring pumps handle wet or particulate-laden gases but tend to be bulkier and consume more power. Customization plays a key role in industries such as food, pharmaceuticals, and chemicals, where production requirements vary widely. Companies like SPX FLOW design and optimize solutions for sectors ranging from agriculture to shipbuilding, ensuring the pump fits the process.
Tip: Always consult with process engineers to align pump selection with production goals and compliance standards.
Total Cost
A comprehensive cost analysis helps buyers avoid surprises over the pump’s lifecycle. The table below outlines the main cost factors:
Cost Factor | Description |
---|---|
Initial Investment | Equipment purchase, durability, and testing expenses |
Installation and Startup | Foundation, utilities, commissioning, and operator training |
Energy | Largest ongoing expense; depends on hours and efficiency |
Operations | Labor for monitoring and running the system |
Maintenance and Repair | Regular service, consumables, and unexpected repairs |
Downtime and Lost Production | Costs from unexpected shutdowns; may justify spare pumps |
Environmental | Handling leaks, hazardous materials, and used lubricants |
Decommissioning and Disposal | Final disposal and restoration costs |
Energy often represents the largest expense over time. Maintenance and downtime can also impact total cost. Buyers should compare lifecycle costs, not just the initial price, to make informed decisions.
FAQ
What is the main difference between oil-sealed and dry vacuum pumps?
Oil-sealed pumps use oil for sealing and cooling. Dry pumps operate without oil, which eliminates contamination risk. Dry pumps suit clean environments, while oil-sealed pumps work well for general industrial use.
How often should a vacuum pump receive maintenance?
Most industrial vacuum pumps require maintenance every 500 to 2,000 hours. The interval depends on the pump type and application. Regular checks help prevent unexpected failures and extend service life.
Can a single vacuum pump serve multiple machines?
Yes, centralized vacuum systems can support several machines. This setup improves energy efficiency and reduces maintenance. However, it may require higher initial investment and careful system design.
What factors affect the total cost of ownership for a vacuum pump?
Total cost includes purchase price, installation, energy use, maintenance, downtime, and disposal. Energy and maintenance often represent the largest expenses over the pump’s lifetime.
Which industries benefit most from dry screw vacuum pumps?
Industries such as semiconductors, pharmaceuticals, and food processing benefit most. Dry screw pumps provide oil-free operation, which prevents contamination and meets strict cleanliness standards.
Post time: Jun-30-2025