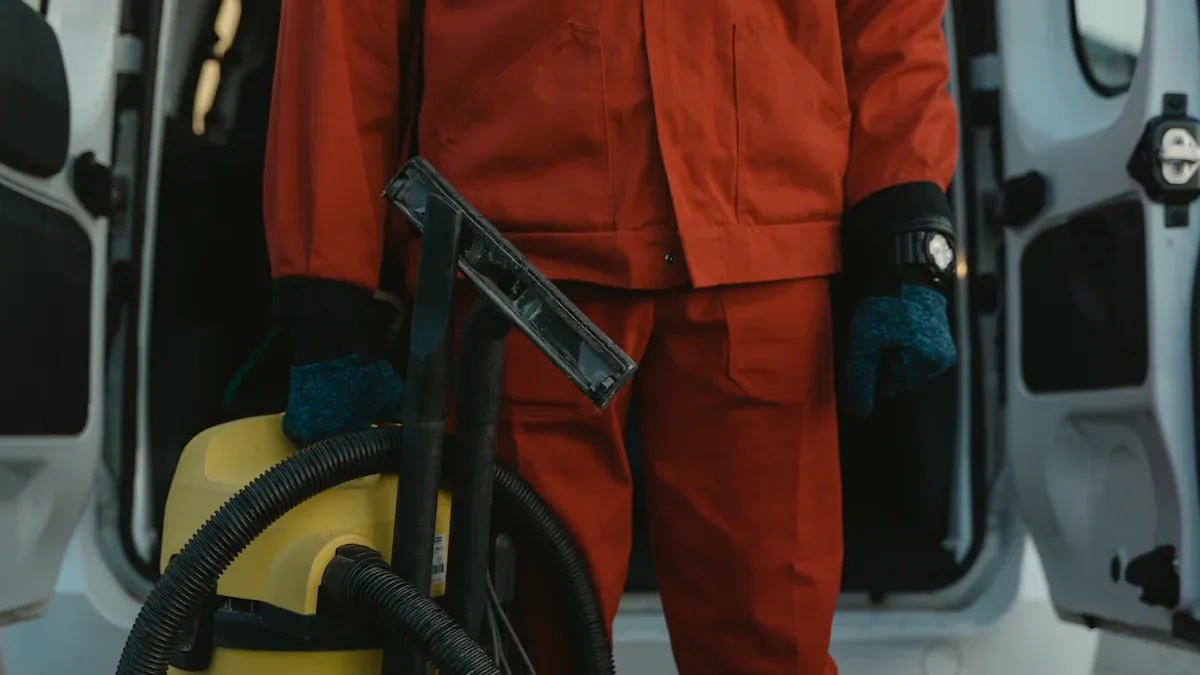
To install and operate a rotary vane vacuum pump safely, follow these essential steps.
Prepare the site and gather the necessary tools.
Install the pump with care.
Connect all systems securely.
Start up and monitor the equipment.
Maintain the pump and shut it down properly.
Always wear personal protective equipment and keep a maintenance log. Choose a good location for your Rotary Vane Vacuum Pump, and follow the manual closely to ensure safe and efficient operation.
Preparation
Site and Environment
You should select a location that supports safe and efficient pump operation. Place the pump on a stable, flat surface in a dry, well-ventilated area. Good airflow prevents overheating and extends the pump’s lifespan. Manufacturers recommend the following environmental conditions for optimal performance:
Keep the room temperature between -20°F and 250°F.
Maintain a clean environment to prevent oil contamination.
Use forced ventilation if the room gets hot, and keep the temperature below 40°C.
Ensure the area is free from water vapor and corrosive gases.
Install explosion protection if you work in hazardous atmospheres.
Use exhaust piping to direct hot air outside and reduce heat buildup.
You should also check that the site allows easy access for maintenance and inspection.
Tools and PPE
Gather all necessary tools and personal protective equipment before you begin. The right gear protects you from chemical exposure, electrical hazards, and physical injuries. Refer to the table below for recommended PPE:
PPE Type | Purpose | Recommended Gear | Additional Notes |
---|---|---|---|
Respiratory | Protect against inhalation of toxic vapors | NIOSH-approved respirator with organic vapor cartridges or supplied-air respirator | Use in fume hoods or vented systems reduces need; keep respirator available |
Eye Protection | Prevent chemical splashes or vapor irritation | Chemical splash goggles or full-face shield | Ensure a tight seal; regular safety glasses are insufficient |
Hand Protection | Avoid skin absorption or chemical burns | Chemical-resistant gloves (nitrile, neoprene, or butyl rubber) | Check compatibility; replace contaminated or worn gloves |
Body Protection | Shield against spills or splashes on skin and clothing | Lab coat, chemical-resistant apron, or full-body suit | Remove contaminated clothing immediately |
Foot Protection | Protect feet from chemical spills | Closed-toe shoes with chemical-resistant soles | Avoid fabric shoes or sandals in the lab |
You should also wear long sleeves, use waterproof bandages on wounds, and select gloves designed for vacuum operations.
Safety Checks
Before installing your pump, perform a thorough safety inspection. Follow these steps:
Inspect all electrical wiring for damage and secure connections.
Check motor bearings and shaft alignment for wear or overheating.
Ensure cooling fans and fins are clean and working.
Test overload protection devices and circuit breakers.
Confirm proper electrical grounding.
Verify voltage levels and surge protection.
Measure vacuum pressure and check for leaks at all seals.
Examine the pump casing for cracks or corrosion.
Test the pumping capacity against manufacturer specifications.
Listen for unusual noises and check for excessive vibration.
Inspect valve operation and seals for wear.
Clean internal components to remove debris.
Check and replace air, exhaust, and oil filters as needed.
Lubricate seals and inspect surfaces for damage.
Tip: Keep a checklist to ensure you do not miss any critical steps during your safety checks.
Rotary Vane Vacuum Pump Installation
.jpg)
Positioning and Stability
Proper positioning and stability form the foundation for safe and efficient operation. You should always mount your Rotary Vane Vacuum Pump horizontally on a solid, vibration-free base. This base must support the full weight of the pump and prevent any movement during operation. Follow these industry-standard steps to ensure correct installation:
Place the pump on a level, stable surface in a clean, dry, and well-ventilated area.
Secure the pump firmly using bolts, nuts, washers, and lock nuts.
Leave enough clearance around the pump for cooling, maintenance, and oil inspection.
Align the pump base with adjoining pipelines or systems to avoid mechanical strain.
Manually rotate the pump shaft to check for smooth movement before startup.
Confirm that the motor rotation direction matches the manufacturer's specifications.
Clean the pump thoroughly after installation to remove any dust or contaminants.
Tip: Always check that the pump is accessible for routine maintenance and inspection. Good access helps you spot issues early and keeps your equipment running smoothly.
Electrical and Oil Setup
Electrical setup requires careful attention to detail. You must connect the power supply according to the motor label specifications. Install a grounding wire, fuse, and thermal relay with the correct ratings to protect against electrical hazards. Before you operate the pump, remove the motor belt and verify the motor’s rotation direction. Incorrect wiring or reverse rotation can damage the pump and void the warranty.
Common mistakes include voltage mismatches, unstable power supplies, and poor mechanical alignment. You can avoid these by:
Verifying the incoming power supply and matching the motor wiring.
Confirming the correct motor rotation before full startup.
Ensuring all breakers and electrical components are rated for the motor.
Oil setup is just as important. Leading manufacturers recommend using vacuum pump oils with properties tailored to your pump model. These oils provide the right vapor pressure, viscosity, and resistance to heat or chemical attack. The oil seals the clearance between the vanes and the housing, which is essential for efficient operation. Before starting the Rotary Vane Vacuum Pump, fill it with the specified oil to the recommended level. Use washing vacuum oil for initial cleaning if required, then inject the correct amount of operational oil.
Note: Always read the manufacturer’s manual for oil type, filling procedures, and startup instructions. This step prevents costly mistakes and extends the life of your pump.
Protective Devices
Protective devices help you prevent both electrical and mechanical failures. You should install quality filters to keep particulates out of the pump system. Avoid restricting the exhaust line, as this can cause overheating and mechanical damage. Make sure the pump has enough airflow to stay cool and prevent oil degradation.
Use a gas ballast valve to manage water vapor and maintain pump performance.
Regularly inspect and replace filters to prevent contamination.
Monitor vane condition and address any signs of wear or overheating.
Regular maintenance of these protective devices is critical. Neglecting them can lead to performance loss, mechanical wear, or even pump failure.
System Connection
Piping and Seals
You need to connect your vacuum system with care to maintain airtight integrity. Use intake pipes that match the size of the pump’s suction port. Keep these pipes as short as possible to avoid restrictions and pressure loss.
Seal all threaded joints with vacuum-grade sealants like Loctite 515 or Teflon tape.
Install dust filters at the pump inlet if your process gas contains dust. This step protects the pump and helps maintain seal integrity.
Tilt the exhaust pipe downward if needed to prevent backflow and ensure proper exhaust flow.
Inspect seals and gaskets regularly. Replace any that show signs of wear or damage to prevent air leaks.
Tip: A well-sealed system prevents vacuum loss and extends the life of your equipment.
Leak Testing
You should test for leaks before starting full operation. Several methods help you find and fix leaks quickly.
Solvent tests use acetone or alcohol sprayed on joints. If the vacuum gauge changes, you have found a leak.
Pressure-rise testing measures how fast pressure increases in the system. A rapid rise signals a leak.
Ultrasonic detectors pick up high-frequency sounds from escaping air, which helps you find fine leaks.
Helium leak detection offers high sensitivity for very small leaks but costs more.
Always repair leaks immediately to keep your system efficient.
Method | Description |
---|---|
Helium Mass Spectrometer | Detects helium escaping through leaks for precise location. |
Solvent Tests | Spraying solvent on components causes gauge changes if leaks exist. |
Pressure-Rise Testing | Measures rate of pressure increase to detect leaks. |
Ultrasonic Leak Detection | Detects high-frequency sound from leaks, useful for fine leaks. |
Hydrogen Detectors | Uses hydrogen gas and detectors to verify gas tightness. |
Residual Gas Analysis | Analyzes residual gases to pinpoint leak sources. |
Monitoring Pressure Changes | Observes pressure drops or changes as an initial or supplementary leak detection method. |
Suction Nozzle Method | Detects gas escaping from the outside using leak detection gas. |
Preventive Maintenance | Regular inspections and replacing sealing compounds to prevent leaks. |
Exhaust Safety
Proper exhaust handling keeps your workspace safe. Always vent exhaust gases outside the building to avoid exposure to oil mist and odors.
Use exhaust filters such as carbon pellet or commercial oil mist filters to reduce smells and oil mist.
Water baths with additives like vinegar or ethanol can help reduce odors and visible mist.
Install condensate separators and vent exhaust out of the workspace to prevent buildup and injury.
Regularly change pump oil and maintain filters to reduce contamination.
Keep exhaust pipes unblocked and properly designed to prevent accumulation of flammable gases.
Never ignore exhaust safety. Poor exhaust management can lead to hazardous conditions and equipment failure.
Startup and Operation
1.jpg)
Initial Run
You should approach the first startup of your rotary vane vacuum pump with care and attention to detail. Begin by double-checking all system connections, oil levels, and electrical wiring. Make sure the pump area is clear of tools and debris. Open all necessary valves and confirm that the exhaust line is unobstructed.
Follow these steps for a safe initial run:
Switch on the power supply and observe the pump as it starts.
Listen for steady, low-pitched operational noise. A typical rotary vane vacuum pump produces noise between 50 dB and 80 dB, similar to the sound of a quiet conversation or a busy street. Sharp or loud noises may signal problems such as low oil, worn bearings, or blocked silencers.
Watch the oil sight glass to ensure oil circulates properly.
Monitor the vacuum gauge for a steady drop in pressure, indicating normal evacuation.
Allow the pump to run for a few minutes, then shut it down and inspect for leaks, oil seepage, or abnormal heat.
Tip: If you notice any unusual sounds, vibrations, or slow vacuum buildup, stop the pump immediately and investigate the cause before proceeding.
Monitoring
Continuous monitoring during operation helps you catch issues early and maintain safe performance. You should pay close attention to several key parameters:
Listen for unusual noises such as grinding, knocking, or sudden increases in volume. These sounds may indicate lubrication problems, mechanical wear, or broken vanes.
Observe the vacuum level and pumping speed. Drops in vacuum or slower evacuation times can signal leaks, dirty filters, or worn components.
Check the temperature of the pump housing and motor. Overheating often results from low oil, blocked airflow, or excessive load.
Inspect oil levels and quality. Dark, milky, or foamy oil suggests contamination or the need for an oil change.
Examine filters and seals regularly. Clogged filters or worn seals can reduce efficiency and cause pump failure.
Track the condition of wearable parts like gaskets, O-rings, and vanes. Replace these parts according to the manufacturer’s schedule.
You can use a simple checklist to keep track of these monitoring tasks:
Parameter | What to Check | Action if Problem Detected |
---|---|---|
Noise | Steady, low-pitched sound | Stop and inspect for damage |
Vacuum Level | Consistent with process needs | Check for leaks or worn parts |
Temperature | Warm but not hot to the touch | Improve cooling or check oil |
Oil Level/Quality | Clear and at correct level | Change oil or check for leaks |
Filter Condition | Clean and unobstructed | Replace or clean filters |
Seals and Gaskets | No visible wear or leaks | Replace as needed |
Regular inspections and prompt action help you avoid costly repairs and downtime.
Safe Use
Safe operation of your rotary vane vacuum pump depends on following best practices and avoiding common mistakes. You should always:
Maintain proper lubrication by checking oil levels before each use.
Prevent debris and fluids from entering the pump by using intake filters and traps.
Avoid running the pump with blocked or restricted exhaust lines.
Never operate the pump with missing or damaged safety covers.
Train all operators to recognize signs of trouble, such as abnormal noise, overheating, or loss of vacuum.
Common operational errors can lead to pump failure. Watch out for:
Mechanical jamming from broken vanes or debris.
Vane sticking due to poor lubrication or damage.
Hydro-lock caused by fluid entering the pump.
Overheating from inadequate lubrication, blocked airflow, or excessive load.
Oil or water leaks from worn seals or improper assembly.
Difficulty starting the pump due to oil deterioration, low temperature, or power supply issues.
Always shut down the pump immediately if you detect abnormal conditions. Address the root cause before restarting to prevent further damage.
By following these guidelines, you ensure safe, efficient, and long-lasting operation of your rotary vane vacuum pump.
Maintenance and Shutdown
Rotary Vane Vacuum Pump Maintenance
You should keep a detailed maintenance log for every Rotary Vane Vacuum Pump in your facility. This log helps you track operating hours, vacuum levels, and maintenance activities. Recording these details allows you to spot performance changes early and schedule service before problems occur. You can prevent unexpected breakdowns and extend the life of your equipment by following a routine maintenance schedule.
Manufacturers recommend the following intervals for key maintenance tasks:
Check oil levels and change oil as needed, especially in harsh or contaminated environments.
Replace inlet and exhaust filters regularly, increasing frequency in dusty conditions.
Clean the pump internally every 2,000 hours to maintain efficiency.
Inspect vanes for wear and replace them if necessary.
Schedule professional maintenance to catch early signs of trouble.
Tip: Always avoid running the pump dry. Dry runs cause rapid wear and can lead to pump failure.
Oil and Filter Care
Proper oil and filter care keeps your vacuum pump running smoothly. You should inspect oil levels daily and look for signs of contamination, such as dark color, cloudiness, or particles. Change the oil at least every 3,000 hours, or more often if you notice water, acids, or other contaminants. Frequent oil changes are critical because vacuum pump oil absorbs moisture, which reduces sealing and efficiency.
Neglecting oil and filter changes can cause serious problems. The table below shows what can happen if you skip this maintenance:
Consequence | Explanation | Outcome for Pump |
---|---|---|
Increased Wear & Friction | Loss of lubrication causes metal contact | Premature failure of vanes, rotor, and bearings |
Reduced Vacuum Performance | Oil seal breaks down | Poor vacuum, slow operation, process issues |
Overheating | Friction generates excess heat | Damaged seals, motor burnout, pump seizure |
Contamination of Process | Dirty oil vaporizes and backstreams | Product damage, costly clean-up |
Pump Seizure / Failure | Severe damage locks pump parts | Catastrophic failure, expensive repairs |
Corrosion | Water and acids attack pump materials | Leaks, rust, and structural damage |
You should also inspect exhaust filters monthly or every 200 hours. Replace filters if you see clogging, increased oil mist, or declining performance. In harsh environments, check filters more often.
Shutdown and Storage
When you shut down your pump, follow a careful process to prevent rust and damage. After use, disconnect the pump and run it open for at least three minutes. Block the inlet port and let the pump pull a deep vacuum on itself for five minutes. This step heats the pump and dries out internal moisture. For lubricated models, this also draws extra oil inside for protection. Turn off the pump without breaking the vacuum. Let the vacuum dissipate naturally as the pump stops.
Note: These steps remove moisture and protect internal parts from corrosion during storage. Always store the pump in a dry, clean area.
You ensure safe and efficient Rotary Vane Vacuum Pump operation by following each step with care. Always check oil levels, keep filters clean, and use the gas ballast to manage vapors. Operate your pump in a ventilated area and never block the exhaust. If you notice startup failure, pressure loss, or unusual noise, seek professional support for issues like worn vanes or oil leaks. Regular maintenance and strict safety practices protect your equipment and your team.
FAQ
How often should you change the oil in a rotary vane vacuum pump?
You should check oil daily and change it every 3,000 hours or sooner if you see contamination. Clean oil keeps your pump running smoothly and prevents damage.
What should you do if your pump makes unusual noises?
Stop the pump right away. Inspect for worn vanes, low oil, or blocked filters. Unusual sounds often signal mechanical problems. Address the cause before restarting.
Can you use any oil in your rotary vane vacuum pump?
No, you must use the oil type recommended by the manufacturer. Specialized vacuum pump oil provides the right viscosity and vapor pressure. Using the wrong oil can cause poor performance or damage.
How do you check for vacuum leaks in your system?
You can use solvent spray, pressure-rise testing, or an ultrasonic detector. Watch the vacuum gauge for changes. If you find a leak, repair it immediately to maintain system efficiency.
Post time: Jul-09-2025